By Tencom Ltd.
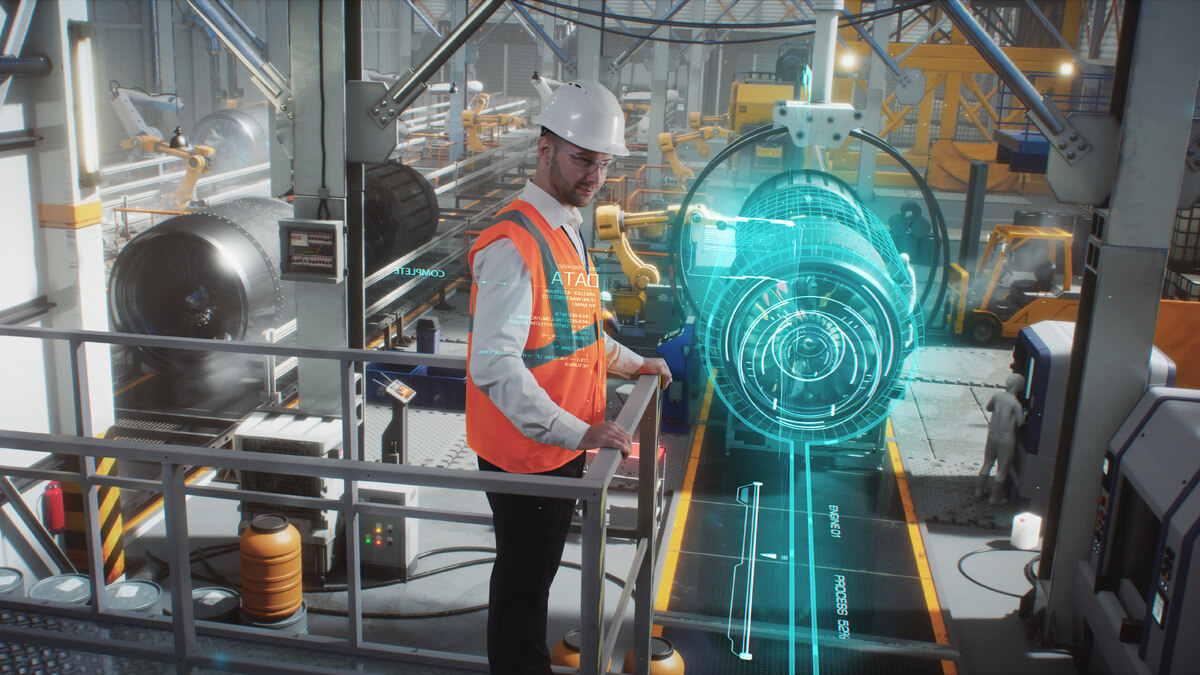
Composite materials have fundamentally transformed the aerospace industry, offering unprecedented weight, strength, durability, and fuel efficiency advantages. These materials, which combine two or more constituent materials with significantly different physical or chemical properties, have become integral to modern aircraft design.
Here’s an exploration of how composites are used in aerospace, their benefits, challenges, and the future of this technology.
What Are Composite Materials?
In aerospace, composite materials typically refer to fiber-reinforced polymers (FRPs):
-
Fibers: Often carbon, glass, or aramid (Kevlar), providing strength and stiffness.
-
Matrix: Polymers like epoxy or thermoplastics, which hold the fibers in place, transfer loads, and protect against environmental damage.
Applications in Aerospace
1. Airframes and Structures:
-
Primary Structures: Fuselage, wings, and tail sections. The Boeing 787 Dreamliner and Airbus A350 XWB extensively use composites, with over 50% of their structure made from these materials.
-
Secondary Structures: Interior panels, seat frames, and fairings where weight savings are also beneficial.
2. Engine Components:
-
Fan blades, casings, and nacelles benefit from composites' resistance to high temperatures and their ability to dampen vibrations.
3. Satellite and Spacecraft Structures:
-
Used for solar panels, antennae, and structural components due to their lightweight nature and resistance to space conditions.
4. Propulsion Systems:
-
Composites are used to construct rocket nozzles and fuel tanks, where weight and thermal properties are critical.
Benefits of Composite Materials in Aerospace
-
Weight Reduction: Lower weight directly translates into less fuel consumption and higher payload capacity or range.
-
Corrosion Resistance: Unlike metals, composites do not corrode, leading to lower maintenance costs and longer service life.
-
Design Flexibility: Composites can be molded into complex shapes, allowing for aerodynamic efficiency and structural integration.
-
Fatigue Resistance: They typically have better fatigue resistance, crucial for the cyclic loads experienced in flight.
-
Thermal Insulation: Composite materials can provide better insulation, impacting both cabin comfort and system efficiency.
Challenges
-
Cost: Manufacturing composites can be expensive due to the complexity of processes like autoclave curing or resin transfer molding.
-
Repairability: Repairing composites can be challenging, often requiring specialized techniques and equipment.
-
Damage Inspection: Damage in composites can be less visible than in metals, necessitating advanced inspection technologies.
-
Recycling: The end-of-life management of composites is problematic, though new methods for recycling or repurposing are being developed.
Future Trends
-
Sustainable Composites: There's a push towards developing composites from renewable or recycled materials to reduce environmental impact.
-
Automation in Manufacturing: Automation, including robotic layup and 3D printing, aims to reduce costs and increase precision in composite production.
-
Smart Composites: Integration of sensors into composite structures for real-time health monitoring is on the rise.
-
Hybrid Materials: Composites can be combined with other materials like metals or ceramics for enhanced properties.
Conclusion
Composite materials have improved the performance and efficiency of aerospace vehicles and pushed the boundaries of design and functionality.
As the technology continues to evolve, we can expect even more innovative applications, further reducing aircraft weight, enhancing durability, and promoting a shift towards more sustainable aviation practices. The future of aerospace seems to be increasingly composite, promising lighter, faster, and more environmentally friendly skies.
Please keep in mind that the benefits outlined in this article could also be applied to other industries.