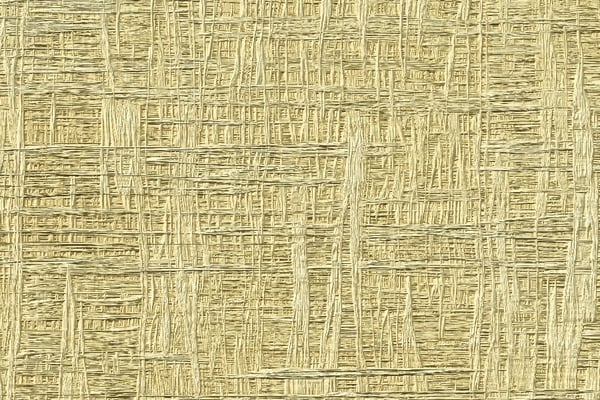
Fiberglass (or glass fiber) is an immensely popular material used across a range of industries that almost everyone – engineers, project managers, or even your Mom – has heard of. It’s lightweight, stronger than most traditional materials, and can withstand extreme environments without corroding, buckling, or warping.
Because of this, it’s used in anything from bridge construction and satellite building to sporting equipment and printed circuit boards (PCBs).
In fact, fiberglass makes up about a fifth of the global composites market. The projected global market value is expected to reach $23.9 billion by 2024.
However, despite being so widely used, the manufacturing process for fiberglass products is relatively unknown.
As such, this article aims to shed light on fiberglass manufacturing – particularly, the manufacturing methods that Tencom uses to produce a range of fiberglass products.
The Raw Materials
There are many types of fiberglass on the market– E-Glass, S-Glass, H-Glass, etc. –the list goes on. Each has different qualities and are distinguished by the different glass fibers used during fiberglass manufacturing.
To create glass fibers, different minerals (silica sand, limestone, kaolin clay, dolomite, etc.) are melted in a furnace until they reach the melting point. Then, the melted glass is extruded through tiny brushings.
These take the form of very small orifices – typically no more than 25 micrometers in diameter. These extrusions are called filaments.
These filaments are then sized (coated in a chemical finish) and bundled into rovings. How many filaments are in a roving and how thick the individual filaments are determines the weight of the glass fibers, which is typically expressed in yield (yards per pound) or tex (grams per km).
An alternative form of glass fiber that is used in fiberglass manufacturing comes in the form of a continuous strand mat. A continuous strand mat is created by dispensing molten glass strands directly onto a moving belt.
As the glass cools and hardens, a binding element is added to keep the product in place. It is then cut and rolled into a long continuous mat.
Pultrusion
Once the rovings or continuous strand mats are formed, they’re bundled up and taken to FRP manufacturers like Tencom where they’re turned into the fiberglass products we recognize and use on a daily basis. This manufacturing process is called pultrusion.
In essence, pultrusion is a process that converts reinforced fibers and liquid resins into fiber reinforced polymer (FRP) composites.
It’s used to create a range of FRPs (carbon fiber, Kevlar, etc), but is most well known for its part in the fiberglass manufacturing.
While there are many ways to create fiberglass products (pultrusion, filament winding, gun roving, etc.), pultrusion is most commonly used and gives superior results in certain applications.
It is because of these benefits that Tencom is known for their pultruded fiberglass products.
Stage 1: Preforming
Before the glass fibers can be impregnated and reinforced by the resin matrix, they must first be preformed and fitted into the pultrusion machine.
To do this, large coils of rovings are pulled through a preformer of tension rollers that get the filaments into a workable shape. In this stage of fiberglass manufacture, the accuracy and continuity of the roving guide are necessary to achieve the strength and quality known of fiberglass.
After preforming, the rovings head for the resin bath to be impregnated with the polymer matrix of choice.
Alternatively, continuous strand mats can be used instead of rovings. That being said, the pultrusion process is largely the same regardless of whether you use a continuous strand mat or rovings. The difference is seen largely in the final product.
Stage 2: Resin Bath
In this stage, the preformed filament rovings (or mats) are saturated in a wet-out resin bath that acts to impregnate the glass fibers with the performance properties required of the specific project.
The composition of the resin bath will change depending on the performance properties required of the finished product, so it’s worth talking to a pultrusion expert to get an understanding of which resin matrix will work best for your project.
However, the resin matrix will almost always include a polymer, pigment, and a catalyst to aid in curing.
Stage 3: Heated Die
Once impregnated, the glass fibers are then pulled through a heated pool where they are cast and set into the desired molds.
The heated pool works to activate the catalyst within the resin and begin polymerizing the product.
It’s an exothermic reaction, so it relies on a constant temperature and once initiated, the temperature of the resin will exceed that of the die.
When done correctly, you’re left with a fully polymerized fiberglass product that is without impurity or imperfection.
Stage 4: Finished Product
Once the pultrusion process is complete, all that needs to be done is to separate the fiberglass from the die and, if needed, to cut the product to size.
When curing, the fiberglass naturally pulls away from the die so separating the composite and the die doesn’t require too much finessing. However, to ensure complete separation of die and product, a hydraulic clump puller is used.
After separation, the fiberglass products are cut to size and shipped to the customer.
Fiberglass can take on many forms due to the malleable nature of the saturated rovings and continuous strand mats.
Whether your desired product is something substantial like a utility pole or rebars for bridge construction, or something smaller like sporting equipment or driveway markers, pultrusion is a fiberglass manufacturing process that can work for you.
Because it’s lightweight, stronger than most traditional materials, can withstand extreme environments with corroding, buckling, or warping, there’s no denying that fiberglass is a brilliant product to use in your next project; there’s no wonder it’s such a popular material.
Hopefully, this article has shed light on fiberglass manufacturing and the diverse nature of the products it creates – particularly the manufacturing methods that Tencom uses to produce a range of fiberglass products.
If you’re looking for a fiberglass manufacturer for your next project or would just like to know more about what pultruded products can do for you, contact Tencom to speak to an expert.